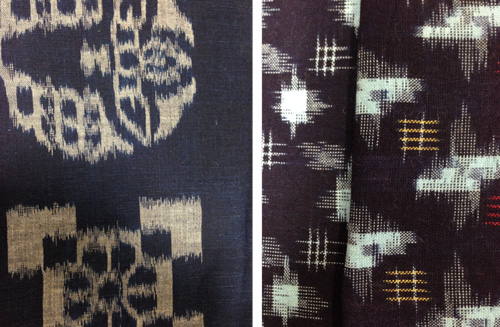
Origin of Bingo Gasuri
“Bingo Gasuri” was first produced about 170 years ago (in 1853, in the late Edo period) in and around the Bingo region, present Fukuyama city, Japan.Katsunari Mizuno, the first feudal lord of Fukuyama Domain, who built Fukuyama castle in 1622, promoted new industries in his domain. Production and sales of cotton fabric was one of them. The land along the coast of the Seto Inland Sea was reclaimed land. Cotton plants are strong against sea breeze. The cultivation of cotton was promoted and then cotton fabric production became popular in farming villages. For young village girls, weaving was a must-have skill to get married. Every night after working in the farming fields, girls and women weaved. In Kannabe, a post town of the Sanyo-do road, durable and affordable cotton fabric they produced sold well. The demand continued to increase. Between 1844 and 1853 some merchants started dealing with cotton and they sold the cotton fabric to even Izumo (a region in present Shimane Prefecture) and Kyushu region. The fabric was called “Kannabe Shima (stripes) or Fukuyama Shima (stripes).”
In 1844, Masahiro Abe, a feudal lord of Fukuyama Domain, enforced laws regulating expenditures and banned the use of silk fabric. In 1853 (in the late Edo period) Commodore Matthew C. Perry of the United States Navy arrived in Japan with his Black Ships. In the same year in the Bingo region, Kyuzaburo Tomita developed and sold new design fabric. A bundle of yarns was wrapped with bamboo sheath and tied with hemp thread. The yarns were tie-dyed and then woven. It is considered the start of beautiful ”Bingo Gasuri.” Bingo Gasuri is one of Japan’s three major Kasuri. The three major Kasuri are Bingo Gasuri, Kurume Kasuri (in Fukuoka), and Iyo Gasuri (in Ehime). Reference Photo: from “NHK Bingo denim in Nippon (Japan)”
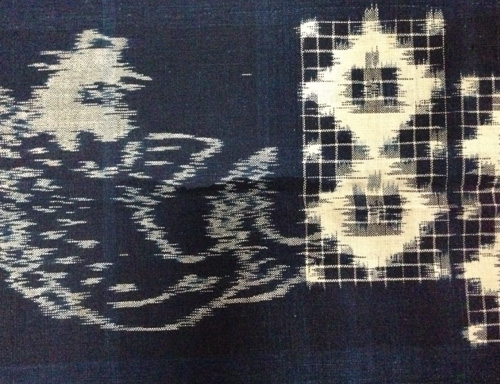
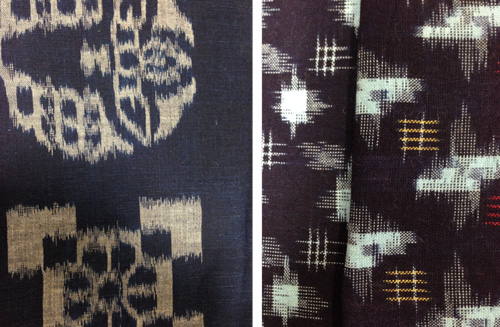
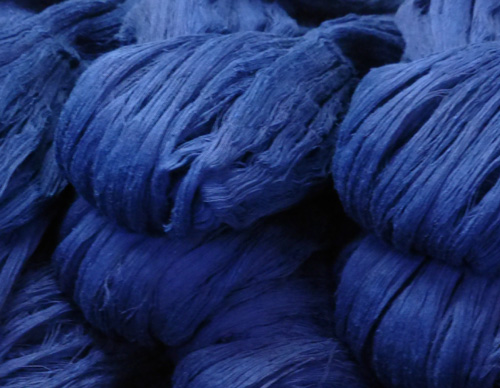
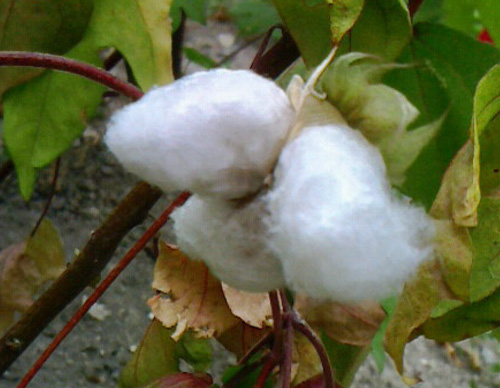
Bingo Indigo-dyed Cotton [Japan Blue]
“Kannabe Shima (stripes) or Fukuyama Shima (stripes)”— fabric woven in Kannabe area from 1622 (Edo period) and distributed widely Bingo fabric has been known for its durability, affordable-price, color fastness, and practical use. Bingo Gasuri was first produced in 1853, and around 1960 the annual shipment reached 3.3 million tan (about 35000 km in length), which accounted for 70% of all cotton fabric production in Japan. Bingo Gasuri Mompe pants, also called Japanese jeans, sold tremendously. Bingo Gasuri’s Japan blue “indigo dye” makes fabric more durable.About Japanblue.
Compared to other countries’ indigo colors, “Japan blue” is deeper and darker. It looks almost black. In the ancient times, cloth dyed in dark or deep blue in a unique way was called “kachi zome” (搗染め, dyeing by tapping cloth) and then it was called “kachi iro” (褐色, blue-black color). In Kamakura period (1185-1333), dark indigo color was called “katsu iro” or “kachi iro” (勝色, literally means winning color). It was treasured by Japanese warrior commanders because of its lucky name and much deeper blue was preferred. Some samurai armors were made with cords dyed in this color. Also, this natural dye helps suppress the growth of germs, so warrior commanders wore clothes dyed in this color to protect themselves from infection. Japanese craftsmen have studied and improved Japan blue color making process and material. Plant leaves called “tade ai” are dried and then fermented by adding natural lye. This special process creates “Japan blue” — one-of-a-kind deep indigo color.Bingo Gasuri is indigo-dyed 100% cotton fabric.
Cotton is moisture-retaining, absorbent and durable material. Cotton is easily dyed in indigo. The textile manufacturers of Bingo Gasuri strictly follow the traditional dying method from the Edo period and use natural indigo dye. Indigo repels insects. During the initial use, the dye may run in water during laundry. It binds to protein of cotton fibers and this chemical reaction makes the fabric more durable.※Wash fabric separately.
Japan indigo-dye fabric has unique “indigo and white” colors.
Denim fades over time. The core of the yarns is white, so the color becomes lighter as you use it. Bingo Gasuri also fades over time. The yarns are dyed to the core. So, indigo color becomes deeper and white color becomes whiter over time.※Some fabric has light-blue color instead of white. It indicates that they are dyed additionally.
※If fabric is exposed to direct sunlight for a prolonged period, the color may fade.
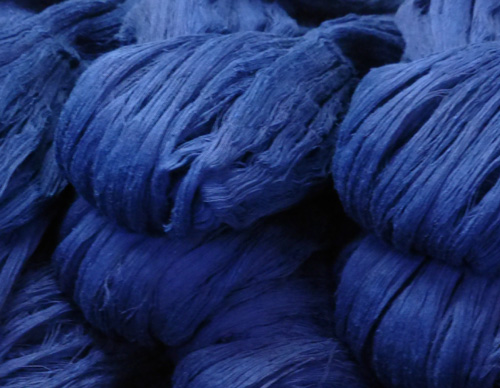
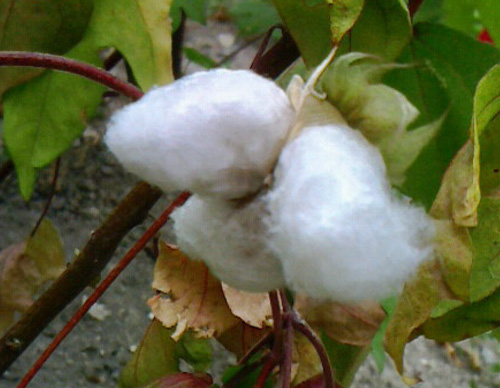
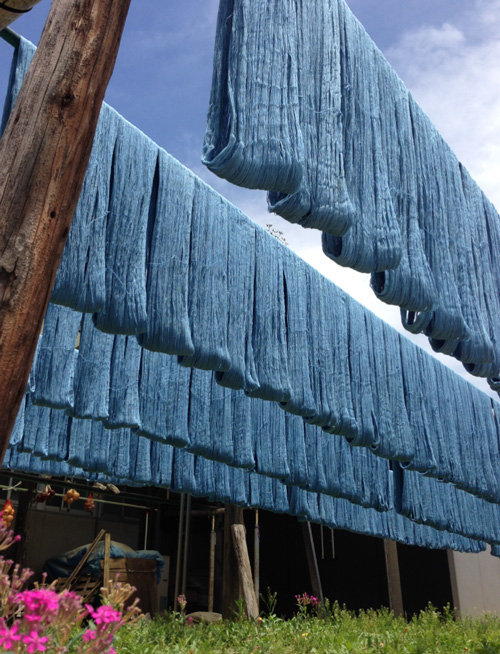
Characteristics of Bingo Gasuri
Kasuri is yarn-dyed woven fabric. A bundle of warp or weft is tie-dyed with indigo or other dye. Weaving tied portion (non-dyed portion) creates various patterns.Fabric Soft to Touch
The yarns are hand-dyed slowly and carefully, washed and dried. Bingo Gasuri’s production processes are time-consuming with detailed work. Multiple processes are repeated over and over to create durable and resilient fabric. Craftsmen often say “Otento-san ni hosanto iken. (I have to dry it in the sun.)” They carefully spread each bundle of dyed yarns under the sun. The yarns are sun-dried slowly, allowing them to hold more air inside. The core of yarn expands, making the fabric soft to touch, cool in summer and warm in winter. Even with the same natural dye, the finish color is slightly lighter in summer and slightly darker in winter.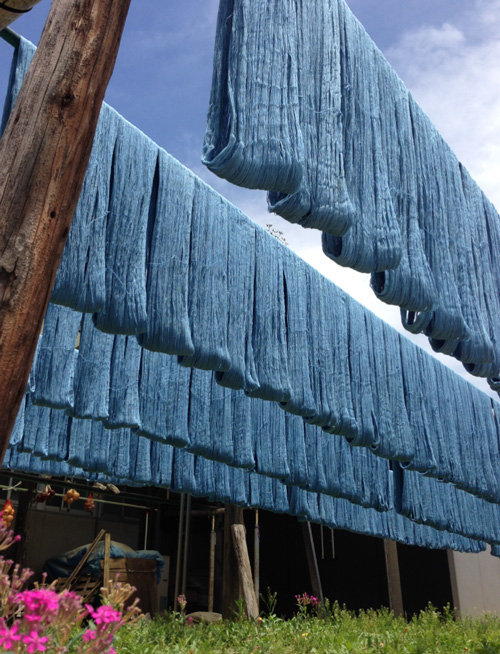
Manufacturing Processes of Bingo Gasuri
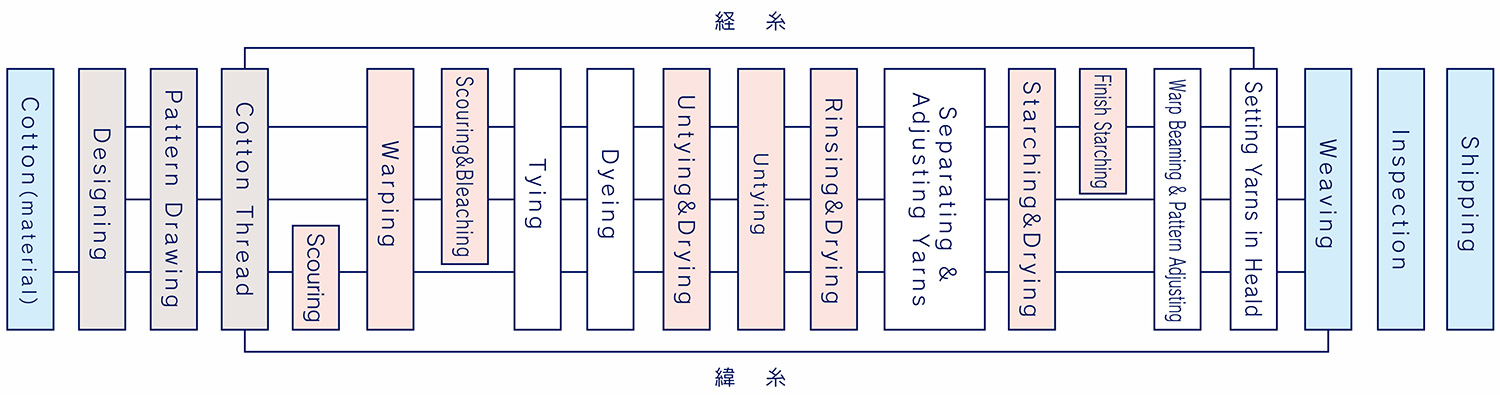
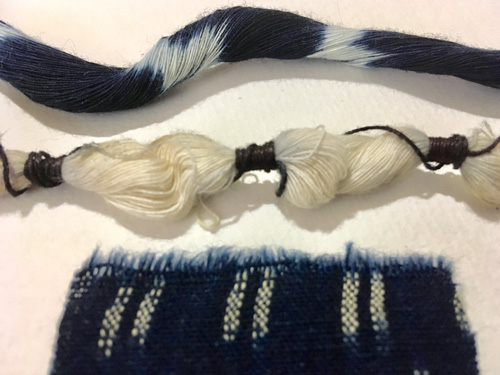
- Designing
- Decide patterns.
- Pattern Drawing
- Design sheet of patterns; Decide where to dye in indigo and where to leave in white.
- Tying
- For each area to be left in white, tie a thread around each bundle of white cotton yarns.
- Dyeing
- Soak the prepared yarns in natural indigo dye carefully. Squeeze the yarns and then.
- Untying
- spread each bundle of the yarns under the sun, allowing them to hold more air inside. (manual process) For light indigo color, repeat this step four times.Untie the thread (black thread in the picture) from the yarns. You will see indigo and white Kasuri yarns.
- Separating & Adjusting Yarns
- Separate yarns, pull and adjust them to create patterns.
- Setting Yarns in Heald
- Set about 2000 warp yarns in a heald of a shuttle loom.
After completing these processes (20 to 40 processes), fabric is produced with a shuttle loom.
※Bingo Gasuri is produced slowly and carefully in 20 processes or more. Originally different manufacturers performed different processes. As the production volume decreased, the division of labor disappeared. Now, there are only two textile companies, which perform all these processes in their own facility. ※When it rains, we cannot dry yarns in the sun. The weather, temperature and humidity affect the shrinkage rate of yarns. They also affect the weaving speed of a shuttle loom. Nature’s rhythm and craftsmanship create the fabric.
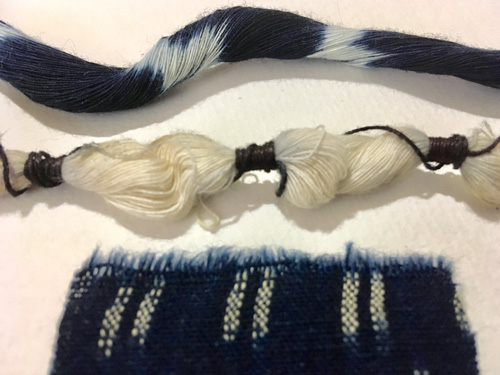
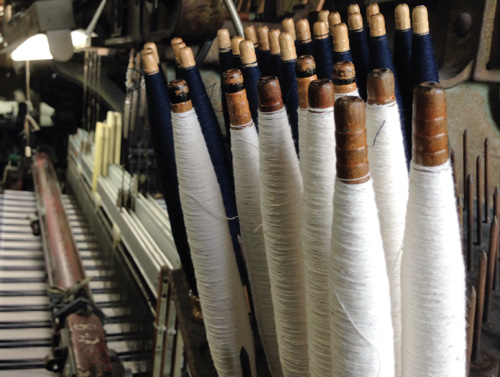
Shuttle Loom
Currently three textile manufacturers use shuttle looms, which were popular in the 1960’s, to produce Bingo Gasuri and Bingo no Momen. This type of loom is hardly produced now. Shuttle looms tend to stop frequently in the rainy season and could operate for 24 hours in the dry seasons. Only skilled craftsmen can handle these tricky looms. Unlike modern looms, the traditional shuttle looms create hand-woven texture. Craftsmen say “Woven fabric goes along with the nature. We cannot rush them.” These fabric making processes are completely opposite of mass-production style. Craftsmen weave them slowly and carefully in 20 processes or more while collaborating with nature. This unique fabric becomes more durable and beautiful in texture with use.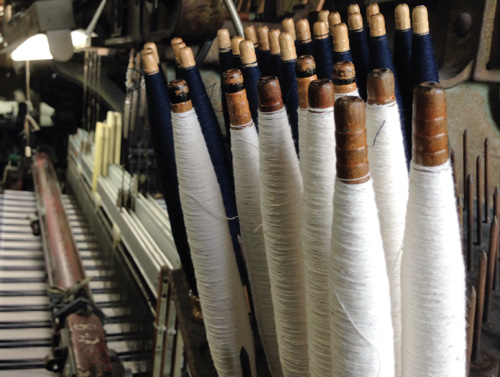